Get Free Estimate
Most commercial roofs are constructed using a built-up roofing (BUR) system consisting of multiple layers, which provides both waterproofing and fall protection. A key element of this BUR assembly is the protective gravel layer installed over the roof membrane.
The gravel serves several important functions, helping to shield the underlying roof components from damage. This article will explore the critical reasons why commercial roofing projects routinely specify a loose stone ballast layer as part of the roofing assembly.
Purpose of Gravel on Commercial Roofs
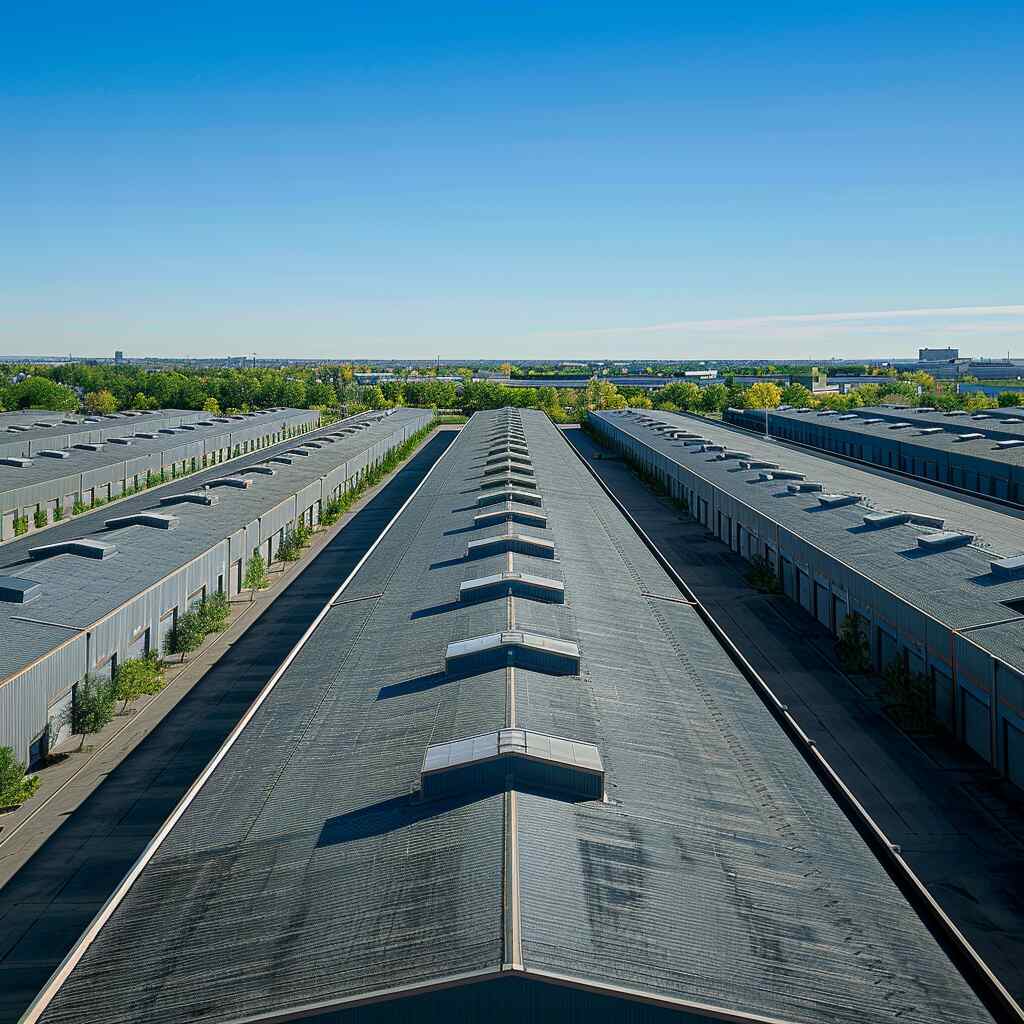
The primary purpose of using gravel as a roofing ballast is to provide protection. The stones are laid over the waterproofing membrane to shield it from regular foot traffic and severe weather. Without the protective gravel layer, foot traffic and wind uplift could puncture or tear the membrane over time. The weight of the gravel also helps secure the roof assembly by retaining it in place should wind gusts or storms occur.
Additionally, the gravel helps to regulate roof temperatures. It reflects absorbed heat from the sun back up into the air, preventing the membrane from becoming overheated. Excessive heat exposure could cause the roof to expand and contract more rapidly which leads to cracking. The stones also shade the membrane from direct sun exposure that causes degradation over many years.
Benefits of Gravel on Commercial Roofs
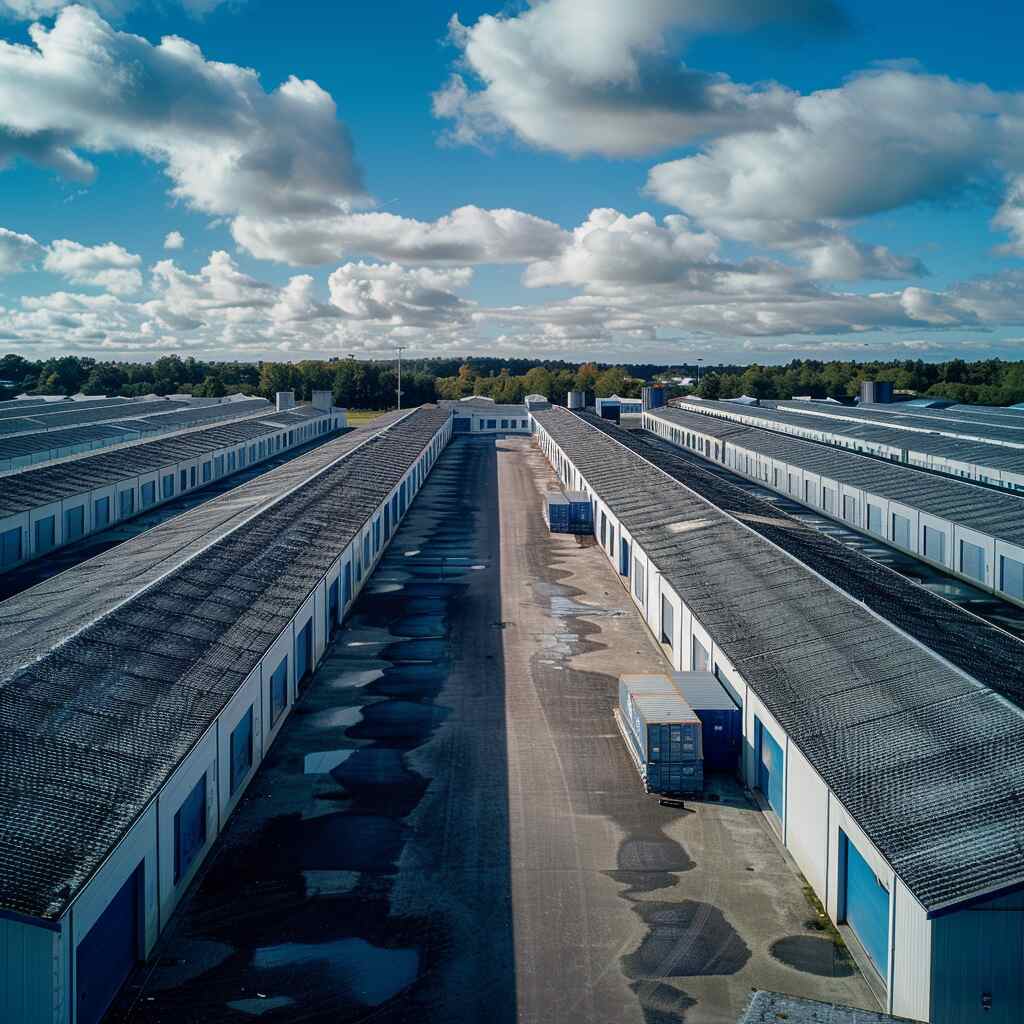
Gravel provides an extremely durable and long-lasting form of roof protection that requires little maintenance once installed. Unlike alternative options, gravel will not wear out, break down or need replacing for the roof’s life. It also withstands abrasion from periodic foot traffic, hail or strong winds, without sustaining damage.
Using a gravel ballast also helps cut energy costs for commercial building owners. The stones reflect sunlight and heat, reducing solar heat gain into the roofing system and, subsequently the interior of the building. This naturally lowers air conditioning needs to maintain comfortable temperatures inside. Less energy expenditure results in significant savings over the long operational lifetime of commercial structures.
Types of Commercial Roofing Systems with Gravel
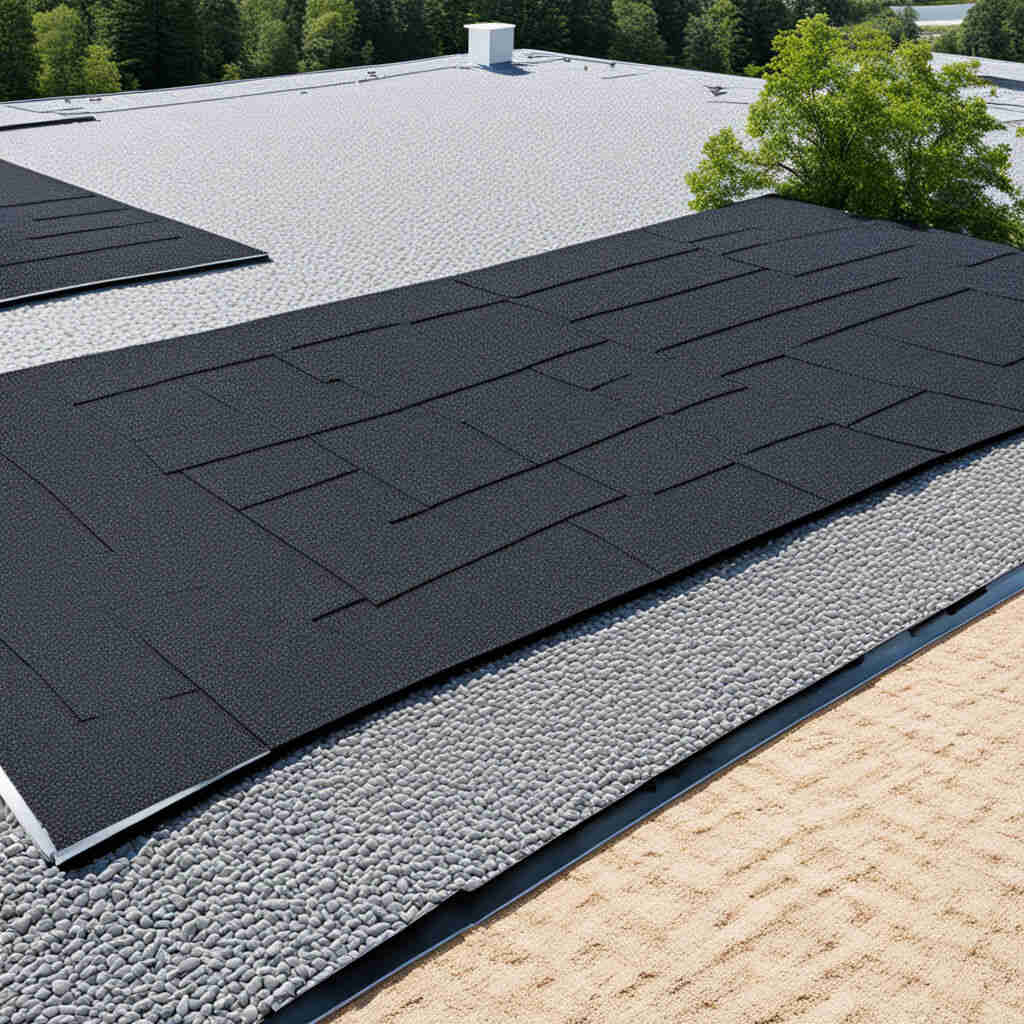
There are several major types of commercial roofing systems that incorporate a protective gravel layer. Modified bitumen roofing utilizes flexible, rubberized asphalt membranes that are fully adhered with hot asphalt or cold-applied adhesive. The completed membrane is then covered in aggregate gravel for shielding from weather and impacts. Tar and gravel roofing, also known as built-up roofing (BUR), is a time-tested system built up in layers of asphalt and felts embedded with aggregate gravel. BUR roofs are extremely durable and can frequently withstand over 50 years of use with proper installation and maintenance.
Aggregate ballasted systems work to securely anchor modified bitumen or BUR membranes beneath a thick layer of washed gravel or crushed stone ballast. This heavy ballast, typically weighing around 25 pounds per square foot, helps to deter wind uplift of the membrane. Another roofing option is a spray foam system, where aggregate is used as a protective barrier to shield the increasingly popular polyurethane foam insulation from weathering, foot traffic, and punctures. A final common commercial roofing type is a composite panel system that utilizes factory-assembled stone-coated membrane panels topped with an additional layer of aggregate for further wind resistance and solar reflectivity benefits. A protective gravel layer plays an integral shielding role across all of these major low-sloped commercial roof designs.
Installation Process and Considerations
While the specific steps vary slightly between different roofing system types, most commercial gravel-covered installations follow a similar general process.
1. First, the roof decking must be properly prepared with any necessary repairs, and cleaning and priming must be completed. The membrane is then fully adhered to the deck with asphalt or an alternative adhesive, ensuring full contact.
2. Subsequent layers are embedded if applicable, such as with built-up roofing. Once the waterproof membrane is fully installed, aggregate is manually scattered uniformly across the entire surface using a placement rate tailored to the size of the stone. Lightly walking across transfers the gravel into the freshly applied asphalt for instant anchoring. The thickness of the final ballast layer depends on specifications but typically averages around 1-2 inches.
3. Factors like roof slope, wind load characteristics, environmental factors and anticipated foot or equipment traffic all influence material selections for both the membrane and stone aggregate. Testing adhesion prior to embedment and verifying full gravel coverage helps ensure the system will achieve the needed uplift ratings and withstand weathering for the desired 15-30-year lifespan. With careful planning and execution, commercial gravel roofs can deliver durable first-cost protection.
Bottom Line
The use of gravel bedding is a defining characteristic of many reliable commercial low-slope roofing systems. The protective stone layer shields membrane roofings from physical damage, temperature fluctuations, and wind uplift – extending the waterproof envelope’s lifespan by decades. While adding material costs, gravel’s benefits vastly outweigh its price through reduced maintenance needs and repair expenses over the roof’s lifetime.
Contractors can utilize various compatible membrane options and specially selected aggregate types, weights, and placements tailored to each job site’s demands and climate exposures. Overall, incorporating a well-installed protective gravel barrier remains a highly effective strategy for commercial buildings to withstand decades of weather with minimal roof investments needed.
CONTACT US
Frequently Asked Questions
Industry standards recommend having your commercial roof inspected at least twice a year, ideally in spring and fall. This allows you to assess any damage from the harshest weather seasons (winter and summer) and catch problems early. However, the frequency can vary depending on your roof’s age, material, and surrounding environment. If your roof is older, flat, or faces harsh weather conditions, you may need more frequent inspections.